
Shell Catalysts & Technologies offers catalysts for both the removal of acetylene in front-end (FE) and tail-end (TE) operations. SC&T is always looking to help our customers decarbonise so achieving startup with minimal flaring is a contribution to these efforts.” We welcome the opportunity to contribute to Hyundai Chemicals’ journey in the energy transition and decarbonisation.
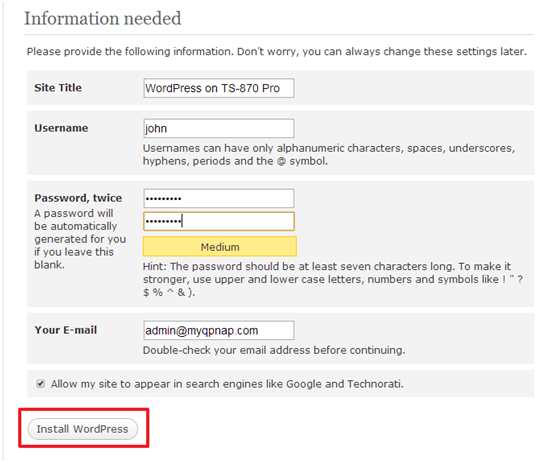
The successful and safe startup with minimal flaring is a significant achievement. We appreciate their dedication to hard work.”Īgnes Lim, Specialty Catalyst Marketing Manager, SC&T, commented, “We are delighted to be part of Hyundai Chemicals’ new developments in the oil-to-chemical arena and to strengthen our long-term relationship with the business. Thanks to Shell’s sophisticated product technology, we were able to achieve early normalisation of the ethylene plant.
#HPC CODE SOURCE CRACKERS PROFESSIONAL#
Ha Chang-Soo, HPC Commissioning Team Leader of Hyundai Chemicals HPC Complex said, “We are very pleased to be able to successfully operate the acetylene reactor with Shell’s excellent catalysts and professional and dedicated technical support. The catalyst also boasts stability features which provide extra confidence in day-to-day operations. These features ensure ethylene producers can gain higher yield from excellent ethylene selectivity. The catalyst has proven to help provide reliable operation at multiple feed sources and various operating conditions. SC&T’s C2 FE selective hydrogenation catalyst was selected by Hyundai Chemicals for the core catalyst unit. It is capable of processing various feedstocks such as naphtha, treated deasphalted oil and refinery off-gas from Hyundai Oilbank’s existing refinery process. Located in Daesan, South Korea, the facility is Hyundai Chemicals’ first heavy-feed grassroot 750 kilotons per annum (KTA) ethylene cracker. hex file).The heavy-feed petrochemical complex (HPC), operated by Hyundai Chemicals, achieved a fast and successful startup in December 2021 by using Shell Catalysts & Technologies’ (SC&T) C2 FE selective hydrogenation catalyst. after making sure we had done our job with success, you will need to make final payment to receive the source code(. After extracting the code, we will send you back two programmed devices for you to test.į.

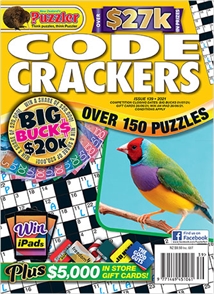
Before extracting the code, you need to pay 50% deposit by Paypal.Į. Ship us the protected device, along with at least two or more not-programmed samples.ĭ. Our staff will response quickest with quotation and delivery time and conditions for service.Ĭ. Please send an inquiry by skype, email or call with description of protected device you have.ī. 3013 Sun Gang East Road, Luohu District, Shenzhen, Guangdong Province, China. These dudes in china don't care about IP protection or patents :( Is there anything in the MAX II or V parts that would make an invasive or semi-invasive attack difficult or is it just a matter of time before they can reverse engineer those ? Maybe someone from Altera can tell us. The thing is, the site I posted the link for is offering that service. So this doesn't change what I said, while it isn't impossible it requires lots of knowledge and equipment, and probably isn't cheap. The only solution I see to get back the data in that case is either through a magical undocumented JTAG command (which I'm not aware of, and I don't think Altera would have done this) or by opening the chip and trying to make that bit change in some way.
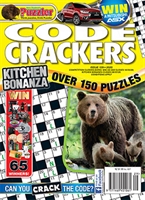
In this case there is no way to access the configuration by probing the power supply or trying to trigger errors that way, as there in no configuration data loading. In that case it makes things a lot harder, as the Max 3000 doesn't use a separate configuration memory but has EEPROM cells directly integrated in the LABs. Sorry I didn't see that you were using a Max 3000A and not a Max V. The question to Altera is have they improved the situation in later devices and what have they done to make this type of invasive chip probing impossible or impractical ? I don't feel happy expending lots of development time only to know that the investment in time and money could easily be given away to some unscrupulous third party :( Until now I was always under the impression that once the security bit was set the security of these devices was bullet proof. Scratching around the internet I found a dude that has done a thesis on the subject and another mob that will actually circumvent the security on these devices and read back the design information so it can be copied by unscrupulous operators !! I'm currently using an EPM3256 CPLD in a prototype to prove a design and was thinking of using the same CPLD in the final revision until a colleague alerted me to possible security vulnerabilities with these devices as well as many other vendor parts.
